The Vertical Reciprocating Conveyor, or VRC, stands out as a game-changer in the vast world of material handling and industrial processes. At its core, a VRC is a specialized lifting mechanism designed to transport goods and materials seamlessly between mezzanine levels. Unlike the elevators we’re familiar with in commercial buildings or malls, VRCs are exclusively dedicated to cargo, ensuring that delicate or robust goods move with utmost care and efficiency.
Table of Contents:
The design of a VRC is a blend of engineering precision and innovation. Typically, it consists of a platform attached to a system of pulleys, counterweights, or hydraulic systems, which facilitate its vertical movement. The absence of a cabin or a dedicated operator space differentiates it from traditional elevators, making it a more compact and efficient solution for vertical transportation.
VRCs are particularly valuable in environments where space is at a premium. Warehouses, manufacturing units, and multi-level storage facilities often face the challenge of optimizing space while ensuring that goods move quickly and safely. VRCs address this challenge head-on, offering a solution that reduces manual labor, minimizes potential damage to goods, and accelerates processes.
Benefits of a VRC
Adopting Vertical Reciprocating Conveyors in various industries isn’t just a trend; it’s a testament to their myriad benefits. Let’s delve deeper into the advantages that make VRCs an indispensable asset.
Customization
One of the standout features of VRCs is their adaptability. Manufacturers often provide customization options, ensuring that the VRC fits the unique requirements of each facility, be it in terms of load capacity, platform size, or vertical travel distance.
Energy Efficiency
VRCs, especially those driven by modern mechanical systems, are designed to consume less power than traditional elevators, reducing operational costs and aligning with green and sustainable business practices.
Safety Enhancements
Beyond the essential safety features, many VRCs come equipped with advanced systems like overload sensors, which prevent the conveyor from operating if the load exceeds its capacity. This proactive approach minimizes risks and potential downtimes.
Integration with Other Systems
VRCs integrate seamlessly with other material handling systems, such as conveyor belts or automated guided vehicles (AGVs), ensuring a smooth flow of goods from one process to another enhancing overall operational efficiency.
Reduced Wear and Tear
Manual transportation methods can often lead to wear and tear of goods, especially from frequent moves. VRCs, with their controlled movement and precise handling, ensure that goods remain pristine during transit.
Scalability
As businesses grow, their material handling needs can change. VRCs offer scalability, allowing companies to upgrade or modify their systems to handle increased loads or adapt to new operational strategies.
VRC vs. Freight Elevator
At first glance, Vertical Reciprocating Conveyors (VRCs) and freight elevators serve the same purpose: transporting goods vertically. However, when we peel back the layers, differences emerge relating to the specific needs and environments. Here’s a comprehensive comparison:
Intended Use and Design Philosophy
VRC | Freight Elevator |
Exclusively designed for cargo, VRCs prioritize the safe and efficient movement of goods. They lack the amenities and controls typical of passenger elevators, focusing instead on robustness and adaptability. | While primarily used for transporting goods, freight elevators can accommodate operators or accompanying personnel. They come with controls and safety features akin to passenger elevators. |
Regulatory Landscape
VRC | Freight Elevator |
Given that VRCs don’t transport humans, they often bypass stringent regulations that apply to passenger elevators, leading to faster approvals and installations. | Subject to rigorous safety standards and regular inspections, freight elevators must comply with many codes and regulations, ensuring the safety of both goods and any accompanying personnel. |
Operational Costs
VRC | Freight Elevator |
Typically, VRCs have lower operating costs. Their design simplicity and energy-efficient mechanisms can lead to significant savings over time. | Due to their complexity and the need to meet strict safety standards, freight elevators can have higher installation and maintenance costs. |
Flexibility and Customization
VRC | Freight Elevator |
VRCs shine in their adaptability. They can be tailored to fit specific spaces, handle unique load types, or integrate with other material handling systems. | While they offer some customization options, freight elevators are generally more standardized due to the regulations they must adhere to. |
Safety Mechanisms
VRC | Freight Elevator |
Advanced VRCs have features like overload sensors, emergency stop mechanisms, and controlled descent systems in case of power failures. | These elevators incorporate safety features that cater to both goods and humans, such as ventilation systems, fire-resistant designs, and emergency communication devices. |
Space Utilization
VRC | Freight Elevator |
With their compact design, VRCs are ideal for locations with limited space. They install in tight spots without compromising their efficiency. | Requires a dedicated shaft and additional space for controls and safety features; freight elevators may demand more real estate within a facility. |
Cost Comparison
VRC | Freight Elevator |
Generally, VRCs have a lower initial investment due to their more straightforward design and fewer regulatory requirements. Operational costs are also typically reduced, given their energy-efficient mechanisms and the absence of a dedicated operator. Maintenance for VRCs, being straightforward and less frequent, further contributes to long-term savings. | The initial investment for freight elevators is higher, factoring in design complexities, the need for a dedicated shaft, and adherence to strict regulations. Operational costs are also higher due to energy consumption and potential operator expenses. Maintenance can be costlier over time due to the need for specialized parts or repairs. |
By understanding these differences, architects, engineers, and developers can make informed decisions, ensuring that their choice aligns perfectly with their projects’ operational needs and constraints. If you need more information about freight elevators, check out this blog post.
VRC Manufacturers
In vertical transportation, the choice of manufacturer and dealer plays a pivotal role in ensuring the reliability, safety, and efficiency of the VRC. While there are several manufacturers globally, a few stand out for their commitment to quality, innovation, and customer satisfaction.
Renowned as the leading manufacturer of American-made VRCs, Autoquip has built a reputation for its engineering excellence and robust designs. Their VRCs are crafted with precision, ensuring durability and optimal performance. Their commitment to quality is evident in every product, making them a preferred choice for businesses seeking reliable vertical transportation solutions.
As a trusted and experienced dealer, American Custom Lifts stands out in the VRC landscape. As an authorized dealer for Autoquip and other American VRC manufacturers, we have solidified our position in the market. By offering American-made VRCs from leading manufacturers, we ensure that clients receive top-tier products backed by unparalleled expertise. Moreover, American Custom Lifts guarantees that your VRC project will meet the ANSI/ASME B20.1 conveyor safety standards and the applicable MHIA guidelines, ensuring compliance and peace of mind. Our dedication to customer satisfaction and the reliability of American-made VRCs make us a go-to choice for businesses across various sectors.
Choosing the proper manufacturer or dealer is more than just a business decision; it’s a commitment to safety, efficiency, and long-term reliability. With American Custom Lifts, businesses can ensure they receive products that stand the test of time and meet industry standards.
Types of VRCs
Vertical Reciprocating Conveyors come in various designs and operational mechanisms, each tailored to specific needs and environments. Here’s a breakdown of the primary types and how American Custom Lifts caters to each category:
Hydraulic VRCs
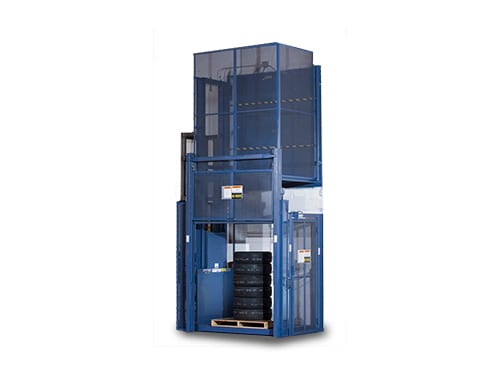
These VRCs use hydraulic cylinders to lift and lower the platform. They’re ideal for applications requiring less frequent lifts and shorter distances. American Custom Lifts provides state-of-the-art hydraulic VRCs, ensuring smooth operation and longevity. Our hydraulic systems are efficient, reduce energy consumption, and perform consistently.
Mechanical VRCs
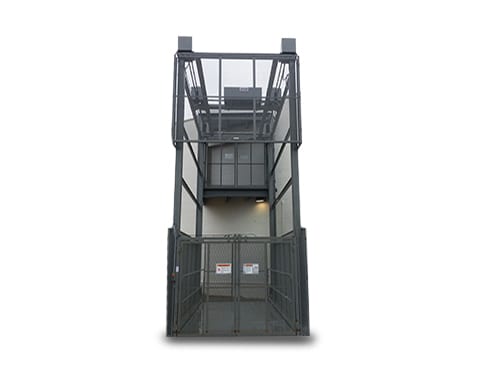
Powered by electric motors and counterweights, mechanical VRCs are suitable for more frequent lifts and longer distances. With a range of mechanical VRCs sourced from top manufacturers like Autoquip, American Custom Lifts ensures that businesses benefit from the latest innovations in mechanical lifting technology. Our offerings are robust, reliable, and designed for high-frequency operations.
Custom VRCs
For businesses with unique requirements, custom VRCs can be designed to fit specific spaces, handle particular load types, or integrate with other systems. Recognizing that one size doesn’t fit all, American Custom Lifts specializes in providing custom VRC solutions. Our team collaborates closely with clients to understand their needs, designing VRCs that align perfectly with operational requirements and spatial constraints.
Choosing the correct type of VRC is crucial for optimal performance and efficiency. With American Custom Lifts’ diverse offerings and commitment to quality, businesses can ensure they find a solution that fits their unique needs.
VRC Design
The design of a Vertical Reciprocating Conveyor is more than just its physical appearance; it’s about ensuring functionality, safety, and efficiency. Each design aspect plays a pivotal role in the VRC’s overall performance.
Load Capacity
VRCs are designed with varying load capacities to cater to different needs. Whether for transporting light goods or heavy-duty industrial equipment, the weight a VRC can handle is crucial. American Custom Lifts offers diverse VRC applications tailored to different load capacities. Our team ensures that each VRC design will handle its designated weight safely and efficiently, catering to the customer’s specific needs.
Platform Size
The size of the VRC’s platform depends on the items it transports. The platform must be spacious enough for safe loading and unloading while optimizing space. American Custom Lifts, with our customer-centric approach, offers customizable platform sizes. Collaborating closely with clients, we determine the optimal platform size to ensure seamless transportation of goods of varying dimensions.
Travel Distance
The distance a VRC can travel, from its lowest to its highest point, is another vital design consideration. American Custom Lifts, leveraging our expertise in VRCs, caters to various travel distances. They ensure smooth and efficient vertical transportation, regardless of the height difference, making them a reliable choice for businesses with diverse needs.
Safety Features
Safety is paramount in VRC design. Each feature ensures risk-free operation, from safety gates and alarms to emergency stop buttons and overload sensors. Our VRCs are a testament to our commitment to safety; equipped with state-of-the-art safety features, they ensure that goods are transported without any hazards.
Integration Capabilities
In today’s interconnected industrial landscape, VRCs must often integrate with other systems like conveyor belts or automated guided vehicles (AGVs). American Custom Lifts rises to this challenge by designing VRCs that can seamlessly integrate with other systems. Our holistic material handling solutions ensure a smooth flow of goods from one process to another, enhancing overall operational efficiency.
With American Custom Lifts at the forefront of VRC design, businesses gain the advantage of solutions that are not only efficient but also tailored to their unique requirements.
Buying a VRC
Purchasing a Vertical Reciprocating Conveyor is an investment that can significantly influence a facility’s operational efficiency and safety. Here’s a guide to making an informed decision.
Assess Your Needs
Before diving into the market, it’s crucial to understand your specific requirements. Consider factors like load capacity, platform size, travel distance, and any unique features you might need. With American Custom Lifts, you’re not just buying a product but gaining a partner. Our team collaborates closely with customers, ensuring the VRC aligns perfectly with their operational needs.
Budget Considerations
While VRCs are an investment, balancing quality with cost is essential. Consider the initial purchase price and potential long-term savings regarding efficiency and reduced labor costs. American Custom Lifts offers competitive pricing without compromising quality, ensuring customers receive value for their investment.
Consult Experts
The world of VRCs can be intricate, and having expert guidance can make all the difference. Engaging with professionals can provide insights into the best VRC for your needs, ensuring you make an informed decision. American Custom Lifts stands out with its seasoned team of experts, ready to offer insights, recommendations, and support, providing customers with the best choice for their facility.
Review Safety Standards
Never compromise safety. Ensure that the VRC you’re considering adheres to industry standards, such as the ANSI/ASME B20.1 safety standards for conveyors and relevant MHIA guidelines. With American Custom Lifts, clients can rest easy. Our VRCs meet and often exceed industry safety standards, reflecting our unwavering commitment to customer safety.
After-Sales Support:
The relationship with a VRC provider should continue after the purchase. Consider the after-sales support, maintenance services, and warranty terms. American Custom Lifts prides itself on our comprehensive after-sales support, ensuring customers have a smooth experience long after the initial purchase. Our dedicated support team is always ready to assist, ensuring the longevity and optimal performance of the VRC.
Investing in a VRC enhances operational efficiency, ensures safety, and optimizes space. With American Custom Lifts as a trusted partner, businesses can be confident in their decision, backed by expertise, quality, and unwavering support.
For further inquiries or assistance, you can contact us during regular business hours via phone. Alternatively, you can email or contact us through our website, which offers both chat support and a web form for your convenience. Our dedicated team is always ready to assist, ensuring you receive timely and comprehensive information for all your VRC needs.
VRC Installation
Installing a Vertical Reciprocating Conveyor is a meticulous process that demands precision, expertise, and a deep understanding of the facility’s layout and operational needs. Here’s a guide to the installation process and the unparalleled advantages of choosing American Custom Lifts.
Site Assessment
Before any installation begins, it’s crucial to assess the site thoroughly by understanding the facility’s layout, identifying potential challenges, and ensuring that the chosen VRC model fits seamlessly. American Custom Lifts begins each project with a comprehensive site assessment, accounting for every detail and tailoring the installation process to the specific environment.
Safety Protocols
Safety is paramount during the installation process. Ensuring that the site is secure, that all personnel receive training, and that the necessary safety equipment is in place is essential. American Custom Lifts prioritizes safety above all else. Our installation teams adhere to stringent safety protocols, ensuring a risk-free installation process for our team and the customer’s facility.
Equipment and Tools
The right tools and equipment can make all the difference in ensuring a smooth and efficient installation. American Custom Lifts utilizes state-of-the-art equipment, installing the VRC precisely and carefully. Our teams train on using these tools effectively, ensuring a swift and seamless installation.
Integration with Existing Systems
For facilities with existing material handling systems, integrating the new VRC can be challenging. American Custom Lifts excels in this area, ensuring that the VRC integrates seamlessly with existing systems, be it conveyor belts, automated guided vehicles (AGVs), or any other infrastructure. Our holistic approach ensures a cohesive material handling solution post-installation.
Testing and Calibration
Once installation is complete, rigorous testing and calibration are essential to ensure optimal performance and safety. American Custom Lifts conducts thorough tests, calibrating the VRC to ensure it operates smoothly, efficiently, and safely. Our commitment to excellence is evident in our meticulous testing procedures, ensuring the VRC is ready for operation.
Training and Handover
After installation, the facility’s team must understand the VRC’s operation and maintenance. American Custom Lifts doesn’t just install and leave; we ensure the customer’s team receives training, is confident, and is ready to operate the VRC. Our training sessions cover operation, safety protocols, and essential maintenance, ensuring a smooth handover.
Choosing the right partner for VRC installation can significantly influence the system’s longevity, safety, and efficiency. With American Custom Lifts’ expertise, commitment to safety, and client-centric approach, businesses receive an installation process that sets the foundation for operational excellence.
VRC Maintenance
Maintaining a Vertical Reciprocating Conveyor ensures longevity, safety, and efficiency. Regular maintenance prevents potential downtimes and optimizes the VRC’s performance over its lifecycle. To further assist our customers, American Custom Lifts partners with a wordlwide network of lift service providers. Here’s a guide to effective VRC maintenance.
Routine Inspections
Regular inspections are the cornerstone of effective VRC maintenance. Periodically checking the system can identify and address potential issues before they escalate. American Custom Lifts offers comprehensive inspection services, where Our trained technicians assess every component of the VRC, ensuring it’s in optimal condition.
Lubrication and Cleaning
Ensuring that moving parts are adequately lubricated, and the VRC is free from debris or obstructions is crucial for smooth operation. American Custom Lifts emphasizes the importance of regular lubrication and cleaning, providing guidelines and services to ensure that the VRC operates without friction or obstructions.
Safety Checks
Safety mechanisms, such as emergency stops, overload sensors, and safety gates, need regular testing to ensure they function correctly. American Custom Lifts conducts rigorous safety checks as part of their maintenance services, ensuring that every safety feature is operational and practical.
Component Replacements
Over time, specific components of the VRC might wear out and require replacement. Using genuine, high-quality parts is essential to maintain the system’s integrity. American Custom Lifts provides authentic replacement parts, ensuring the VRC retains its original quality and performance. Our technicians receive training to replace components efficiently, minimizing downtime.
Software Updates
For VRCs integrated with digital systems or automation, periodic software updates can enhance performance and introduce new features. American Custom Lifts stays updated with the latest advancements, ensuring that VRCs under their care benefit from the most recent software enhancements.
Custom Maintenance Plans
Every facility has unique operational needs, and a one-size-fits-all maintenance plan might not be optimal. American Custom Lifts offers custom maintenance plans tailored to individual client needs, ensuring that the VRC receives care aligned with its usage patterns and the facility’s requirements.
Regular maintenance is the key to ensuring that a VRC remains a valuable asset for a facility. With American Custom Lifts’ expertise, commitment to safety, and tailored maintenance solutions, businesses can be confident that their VRC will stand the test of time, delivering consistent performance year after year.
Conclusion
Vertical Reciprocating Conveyors are more than just machinery; they are the backbone of efficient material handling in countless facilities. Every aspect of a VRC’s lifecycle is pivotal in ensuring operational excellence, from design and installation to maintenance. With the myriad considerations involved, partnering with a trusted expert like American Custom Lifts can make all the difference.
With its unwavering commitment to quality, safety, and client satisfaction, American Custom Lifts has established itself as a leader in the VRC landscape. Our comprehensive offerings, from state-of-the-art VRCs to tailored maintenance solutions, ensure businesses can confidently optimize their vertical transportation needs.
If you’re considering investing in a VRC or seeking expert guidance on maintaining your existing system, take your time. Reach out to the seasoned professionals at American Custom Lifts. Our team is ready and eager to assist, ensuring we meet your VRC needs with the highest standards of excellence.
Remember, in the world of vertical transportation, expertise matters. And with American Custom Lifts, you’re not just getting a product; you’re gaining a partner dedicated to your success. So, don’t wait. Contact us today and elevate your material handling operations to new heights.